A leading provider of construction equipment machinery, JCB’s main goal is to deliver the best level of customer service in the industry.
With a global network of 14 distribution centers and more than 2,000 dealer locations, JCB has some of the top engineering facilities in the world producing a range of more than 300 unique machines. JCB implemented Syncron Inventory to achieve improved service parts availability – ensuring all service parts are quickly delivered to customers when and where they need them.
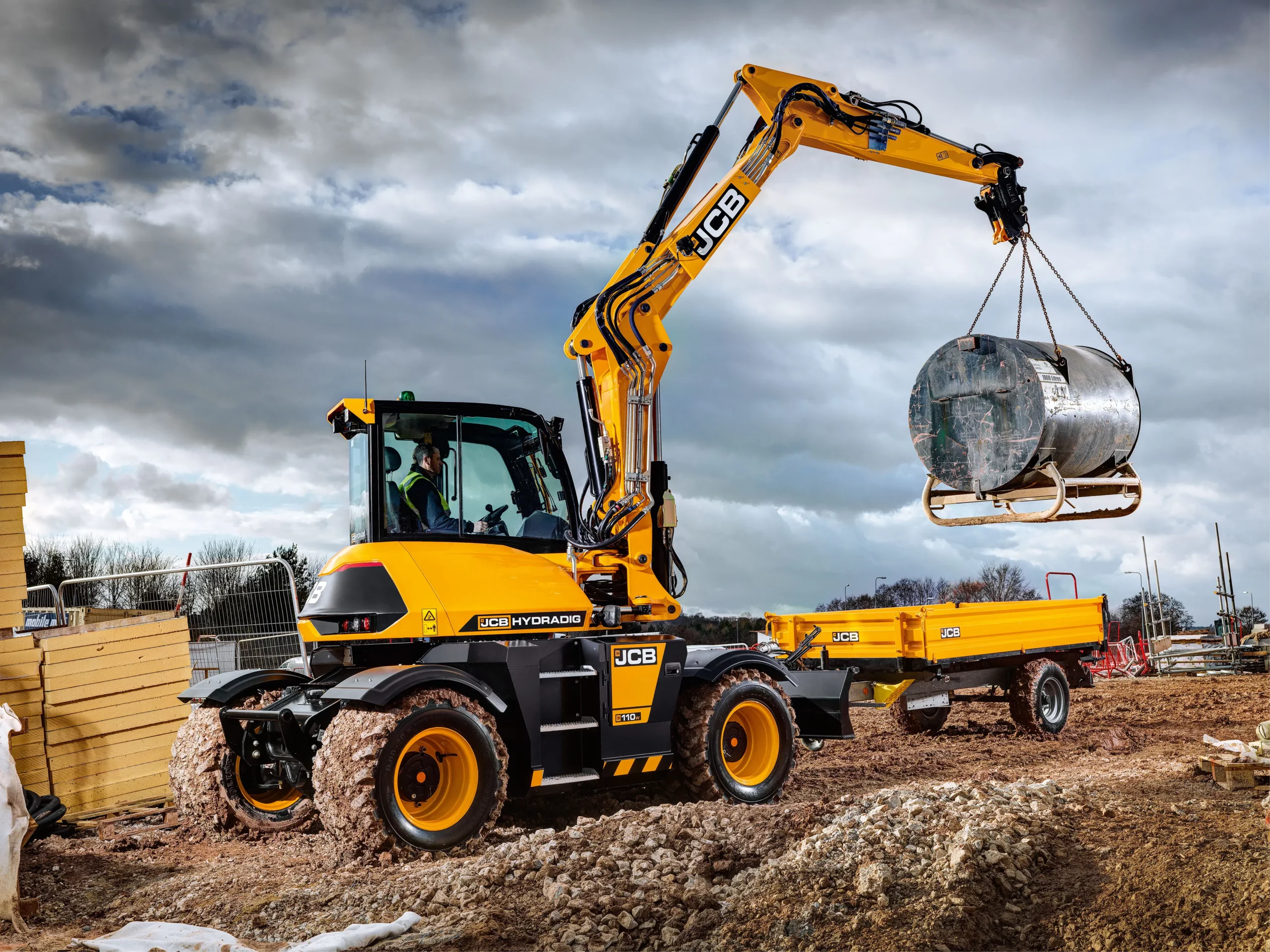
Challenges
Because of their global reach, the JCB team was challenged with a complex supply chain consisting of multiple ERP systems and fragmented, manual processes for parts management. Planners didn’t have visibility into supply or demand between different stocking locations, leading to forecast accuracy issues and problems maintaining a balanced inventory. With the ultimate goal of improving customer service, they sought a single, integrated and streamlined solution for service parts management.
Solutions
To solve this service parts problem, and to finally establish a clear view of its global inventory, JCB began the search for a solution capable of providing greater control and visibility, as well as an effective inventory redistribution process that eliminates overstocking and enables warehouses to work with each other to meet demand. Syncron Inventory allowed JCB to reach record high levels of uptime with minimal risk and increased its customer service levels by nearly eight percent.
Results
With a centralized parts planning process, JCB customers now get the right part when they need it, wherever in the world they might be. Managed by a newly formed central planning team, Syncron Inventory has automated the majority of the service part planning process, enabling JCB’s planners to focus on managing exceptional items and spend more time on value-adding activities. Greater inventory control means improved inventory redistribution, ultimately eliminating overstocking by empowering warehouses to work together to meet demand efficiently.
- 7.4% point increase in customer service levels from improved parts availability.
- Complete visibility and control of inventory at each stocking location.
- A centralized parts inventory planning process with quicker reaction to changes in demand.
- Reduced manual effort from automated and exception-based inventory management.