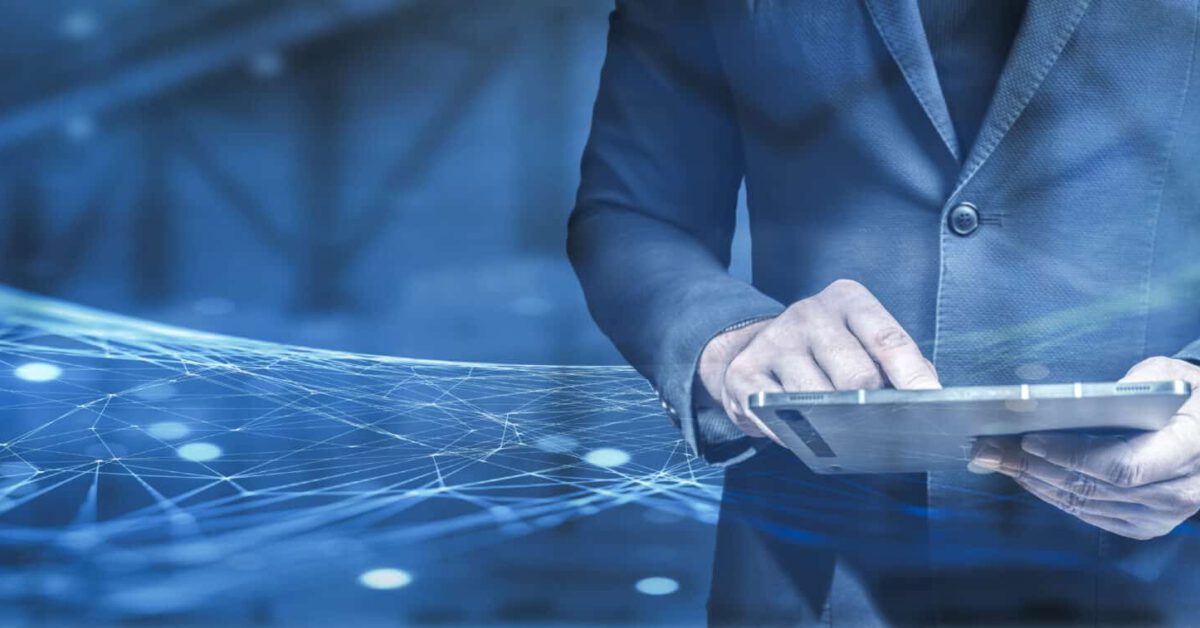
The turbulence of the past few years has created an unprecedented set of hurdles for supply chains and service organizations around the world. From sourcing disruptions and stoppages to rising costs and shifting customer expectations, there’s no doubt that today’s successful business models don’t look the same as they used to.
For service organizations, staying a step ahead of the competition means leveraging predictive, intelligent planning platforms to transform their challenges into opportunities. By harnessing the power of a connected service ecosystem, service leaders can minimize shock, increase agility and become more resilient across their supply chains. Here are the benefits of prioritizing supply chain planning (SCP) and how it can help transform your service organization into a connected, holistic operation.
1. Minimize maintenance challenges
Effective maintenance and field service management are fundamental for service organizations to help customers faster than their competitors can. Field service teams must deliver timely maintenance that increases uptime and improves efficiency.
Predictive analytics can help identify potential breakdowns and other issues before they become problematic. By knowing when a machine was last serviced and then automating the scheduling process, service organizations can save time and money, ultimately catching problems before they occur and delivering on their promises to their customers.
Smart technology can help field teams easily detect when machinery is inefficient or malfunctioning, giving time for preventive steps to fix the issue before it escalates. Adopting connected maintenance solutions enhances operational efficiency, resulting in streamlined, responsive service quality and increased customer satisfaction.
2. Create smoother supply chains
Recent supply chain disruptions have exposed the vulnerabilities of global supply networks, highlighting their gaps and inefficiencies in delivering goods and services. But with the support of agile SaaS solutions built specifically for the supply chain, service leaders can automate parts ordering, reduce customer wait times and plan ahead of service demands. These capabilities allow service organizations to proactively plan and manage their inventory, extend lead times and get ahead of parts shortages and backorders.
A unified approach to SCP also prevents oversupply and over-ordering, resulting in smoother revenue and cost flows for both OEMs, distributors, and their customers. By optimizing supply chain operations through smarter, more connected planning, service organizations can work more efficiently, reduce obsolete inventory and enhance the overall service experience.
3. Anticipate cost pressures and market uncertainties
According to a recent survey on the current state of aftermarket service, 99.6% of service and supply chain leaders across Europe and the United States who responded report significant challenges with parts pricing optimization. Most (60%) of those surveyed also shared that their organizations use manual or custom-built solutions to manage these processes.
Predictive pricing is a powerful tool that can help service organizations capitalize on new service business models while simultaneously ensuring optimal pricing strategies. By using data and insights from a connected planning ecosystem, service organizations can make informed decisions on pricing for equipment and services, avoiding paying too much or charging too little.
This proactive approach helps service organizations effectively navigate cost pressures and market uncertainties, driving greater profitability and competitive pricing for exceptional aftermarket services.
4. Maximize efficiency to drive sustainability
Efficiency and sustainability go hand in hand. Connected planning platforms equip service organizations with the data and insights they need to reduce material usage and waste, as well as improve the environmental impact of shipping.
With a holistic view of the supply chain and all operational processes, service organizations can proactively plan and easily pivot as needed, optimizing resource utilization and minimizing environmental impact. This comprehensive approach not only drives operational efficiency it also aligns with sustainability goals, making service organizations more socially responsible and environmentally conscious.
Intelligent planning is essential for service organizations to thrive in today’s dynamic business landscape. Adopting a holistic, proactive approach to service operations through connected planning can enhance service quality, customer satisfaction and overall performance.
By unifying mission-critical processes across operational and data silos with a common data mesh, Syncron helps service organizations achieve a seamless, efficient service value chain. Embrace service transformation with Syncron and stay ahead in today’s competitive landscape.