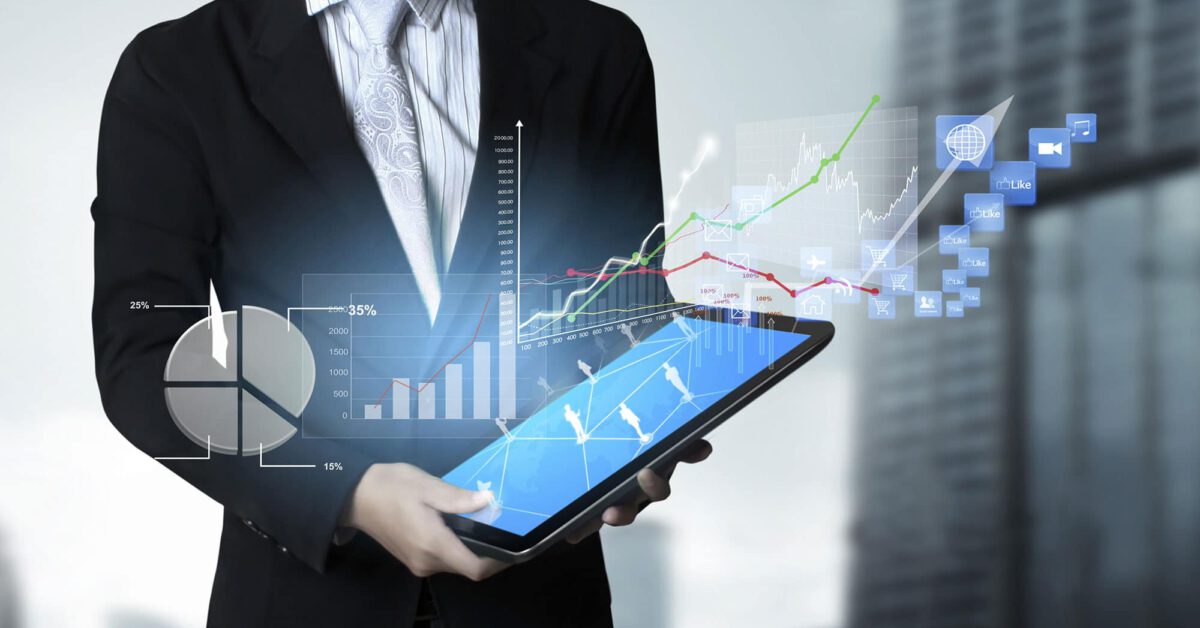
Have you ever wondered how life would be if we could test all of our decisions before we made them? What about if you could look back on decisions you made a year ago and simulate how a different decision would have impacted the results? Having these options would be like having a crystal ball and a rearview mirror all in one – and that’s exactly what an inventory replay simulator does for original equipment manufacturers (OEMs). With an advanced replay simulator, OEMs can change any inventory optimization configuration and simulate how the change would have impacted their service and inventory results.
But, what’s the true value of this information? Simply put: this kind of predictive and/or retrospective information better equips OEMs with the ability to forecast the impact of future strategic inventory decisions.
Why Part Availability is Crucial to Competitive Success
When it comes to after-sales service, there are many reasons that can lead customers to stray from the OEM to a third-party provider. Price, speed and efficiency and part availability all play a role in the customer’s satisfaction with an OEM.
But, because the margin of error for customer satisfaction is extremely narrow in today’s climate, optimized part availability – from the replacement part down to all the parts necessary to complete the service – is absolutely critical for OEMs looking to provide efficient and competitive service.
The True Value of Looking in the Rearview Mirror
But optimized part availability isn’t just about stocking shelves with more parts, it’s about stocking them with the right parts. For example, say there was a customer order that wasn’t fulfilled because a specific part was listed as back-ordered. The likelihood of that customer going elsewhere for that specific part is extremely high not only for that original order, but potentially for orders in the future – even if those future parts are available.
In fact, poor part availability reverberates throughout the entire supply chain; whereas optimized part availability can help OEMs avoid expedite costs, not to mention unbelievably expensive, heroic efforts to meet customer satisfaction levels.
That’s why having an advanced inventory replay simulator to be able to look back on a previous service experience and then use that information to assess the impact that a different stocking decision would have made on the end result could be the make or break success factor in service parts planning.
Proactive Parts Planning: Replay Simulator or Crystal Ball?
Of course, retrospective information is critical to growth – if you can’t measure it, you can’t improve it. But what if OEMs had a way to test stocking decisions before they’re made to properly stock parts ahead of time? Lucky for them, an advanced inventory replay simulator also has the ability to proactively run “what-if” scenarios that do just that.
By simply plugging different scenarios into the simulator, OEMs can essentially pick which scenario seems the most risk averse, which is least disruptive to the overall supply chain – even determining what to do in the case of a problem or emergency.
This is also valuable in terms of looking at the benefits of compliance within the system; with a replay simulator, OEMs can look at instances where parts planners have manually intervened and overwritten the system to either order (or not order) based on specific scenarios. This information allows OEMs to compare how that decision would play out versus if they had let the inventory management system make the stocking choice.
In many cases, manual intervention results in increased excess inventory in the future, ultimately driving home the value of an optimized inventory planning solution. And, at the end of the day, if OEMs are still managing their inventory manually instead of with intelligent service parts planning solutions, they risk losing out to third-party providers. And, in an industry where competition is high and customer expectations are even higher, OEMs are going to need to use every tool in the shed to stay ahead.
–
Interested in learning more about how to start your journey toward better inventory optimization for your organization? Reach out to us today to speak to an expert about how you can get started with an intelligent inventory management solution that meets the needs of your business today and will evolve with you into the future.