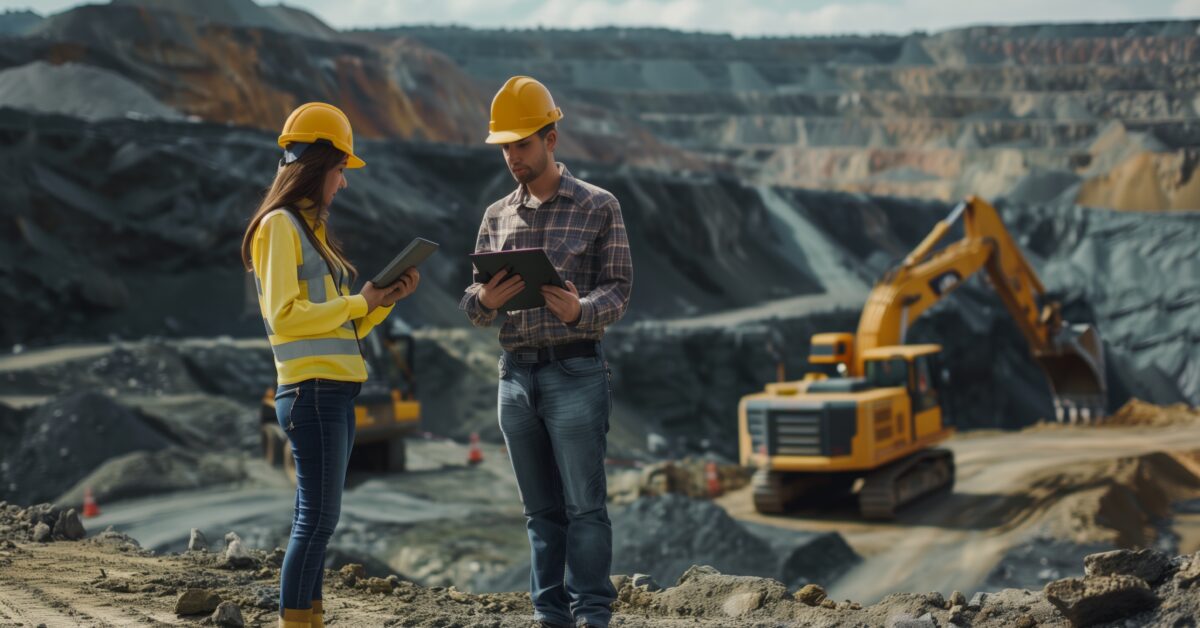
Higher costs, high interest rates, supply chain issues and other concerns have presented notable challenges for the construction industry over the last year.
And manufacturers in the construction world are having to meet growing consumer pressure from three angles:
- Rising customer expectations: Nowadays consumers expect high-quality, reliable products from brands they can trust and that have a long product life. If equipment is unreliable and the repairs process is slow, clunky and costly, customers will lose trust and defect to other manufacturers that take their costly downtime more seriously!
- A shift in customer preferences away from owning and towards leasing: What customers really want is not to own a particular piece of equipment (and the associated maintenance) but to get a certain outcome (i.e. an MRI scan or a big hole in the ground), which is leading to new models based on renting or leasing equipment alongside contracts to have them serviced and maintained by the manufacturer (or one of their dealers)
- The imperative for environmental sustainability: There is growing demand to reduce e-waste and make the manufacturing process as sustainable as possible (major manufacturers such as Caterpillar have committed to a Circular Economy approach, for example).
How can manufacturers secure future growth in the face of these pressures?
One way of simultaneously meeting these pressures is depot repair: the return, refurbishing, and restoration of construction equipment to optimal functionality.
For example, Caterpillar is focusing on developing better systems to optimize use of resources, maximize the total life cycle value of their products and minimize the cost of ownership for their customers.
They have an innovative remanufacturing program to refurbish end-of-life products to same-as-new condition as well as a rebuilding program to upgrade products with new parts to increase their lifespan at a fraction of the cost of a new machine.
These provide customers with lower-cost products, shorter periods of downtime and quick, dependable service options.
(See our eBook How The Circular Economy Is Unleashing New Sources Of Business Value In The OEM Industry for more insights).
So what does depot repair involve?
The core pillars of depot repair
Depot repair in the context of the construction industry refers to the process of repairing and refurbishing equipment that has been sent to a specialized service center or facility.
It is, however, a complex undertaking involving several key processes:
- Inventory and supply chain management: Procurement of parts and materials, managing stock levels, coordinating the movements of parts (including returns to suppliers).
- Scheduling equipment repairs (and engineers): Prioritizing repairs based on warranty, contract status etc., assigning engineers based on availability, skills etc., estimating how long repairs will take and optimizing workflows.
- Managing repair contracts and customer service: Outlining contracts (pricing, warranties, timelines), communicating regularly with customers and handling claims, ensuring that repair work meets customer expectations.
- Tracking repair progress: Using software to track progress of equipment, providing insights into repair volumes, analyzing repair data to identify trends, improve processes and reduce future repair needs through better preventive maintenance practices.
- Advanced exchanges: This model sees the OEM send the customer a replacement unit when their equipment is sent to the depot for repair (like a loan car you would get when yours is in the shop) in order to minimize downtime and maximize customer satisfaction.
These aspects of depot repair collectively ensure that the service is efficient, reliable, and responsive, ultimately leading to higher customer satisfaction and better management of resources.
Benefits for the construction industry
Effective depot repair plays a critical role in balancing operational costs with customer satisfaction.
It helps businesses to streamline and optimize the repair process, eliminating delays and inefficiencies in order to minimize expenses and repair turnaround time.
This has substantial long-term benefits for end customers, helping manufacturers to secure future equipment sales and—most importantly—lucrative, high-margin service contracts:
- Maximized productivity: Ensures that equipment operates at peak performance levels by focusing on reliability and uptime, leading to more efficient job completion and reduced downtime.
- Cost efficiency: Delivers the lowest total owning and operating life cycle costs through cost-effective performance options and a variety of repair solutions tailored to service needs.
- Investment value: Enhances return on investment by providing higher resale values and like-new warranties, making the equipment more valuable over its lifetime.
- Resource preservation: Supports environmental sustainability by preserving the majority of the energy and materials required to manufacture the original component or machine, reducing the need for new resources.
Challenges for the construction industry
Construction equipment is generally incredibly complex with many thousands of parts and the supply chain that supports the repair process is vast. The sheer volume and complexity of the process can cause innumerable delays and bottlenecks.
Here are a few of the key pain points that equipment manufacturers struggle with:
- Repair status and tracking: Tracking the status of parts, materials and equipment through the repair process is challenging, resulting in delays and difficulties identifying bottlenecks or areas for improvement.
- Repair cost and complexity: Modern construction equipment is complex with advanced components, requiring skilled technicians and diagnostic tools, which can be costly to maintain (especially in the face of inefficiencies in the repair process). They can suffer from a variety of issues, from simple wear and tear to complex electronic failures or software problems. Each type of repair may require different expertise, tools, and parts, increasing the complexity of managing depot repair operations.
- Unpredictable supply chains: Variables outside of your control (e.g. weather, political events, transport delays, supplier issues) can impact your supply chain, making planning more challenging. Similarly, poor communication and coordination between partners and stakeholders can exacerbate these issues.
- Customer expectations and retention: Efficiently managing the logistics of receiving, repairing, and returning construction equipment on a tight schedule requires robust scheduling and tracking systems, which can be complex and expensive to implement and maintain. Similarly, maintaining effective communication with customers throughout the repair process is crucial but can be resource-intensive.
By effectively managing depot repairs, companies can sustain a loyal customer base and reinforce their position in a competitive market.
How Syncron can help you with depot repair
Syncron’s Depot Repair & Reverse Logistics Solutions enhance the depot repair process with several key capabilities.
These include:
- Optimized asset recovery and cost management: The system effectively manages asset recovery rates, helping to reduce expenditures on new parts and increasing depot efficiency.
- Logistics and RMAs optimization: Syncron’s solution minimizes logistics costs and enhances visibility into RMAs, streamlining the entire returns process.
- Transformative customer experience: By simplifying returns and repairs, Syncron converts potential negative experiences into positive outcomes, boosting customer satisfaction and loyalty.
- Support for the circular economy: Aligning with sustainable practices, the solution promotes the return, repair, and reuse of parts, contributing to an environmentally responsible business approach.
- Operational excellence with inspections: Syncron’s system includes features for inspections to record and track repair activities against predefined workflows to ensure high-quality repairs and maintain consistency across operations.
- Comprehensive solution for depot operations: From automated tracking and optimized inventory to streamlined logistics and efficient repair management, Syncron provides a robust solution for improving depot repair and reverse logistics.
Case Study: Transforming depot repair for a leading electronics equipment manufacturer
Now let’s look at a real-life example of how Syncron helped a leading electronics manufacturer (with $13bn revenue) to optimize its depot repair service.
The challenge
The manufacturer faced the challenge of managing a massive volume of repairs annually.
And they faced a number of challenges that were adversely affecting the customer experience:
- Difficulty processing refunds and notifying customers: A complex payment structure for repairs led to customer frustration around handling refunds with a requirement for an automated system to notify customers and authorize payments.
- Limited range of suppliers: In order to maintain control of intellectual property the client was managing depot repair in-house or with only a limited set of vetted suppliers.
- Logistical shipping difficulties: Ensuring equipment was returned to the correct location required proactive issuance of Return Merchandise Authorizations (RMAs), accurate collection of shipping information, provision of necessary return materials to customers and diligent tracking of shipments and receipts.
- Costly manual tracking systems: Paper-based tracking of repair processes was costly and inefficient.
The solution
Syncron introduced a comprehensive software solution to help the client meet these challenges, including an integrated payment system, a robust shipping system, an inspection function to streamline workflow management and a digital tracking system to replace the paper-based one.
Here are the details and the business impact of each:
Solution | Description | Impact |
Integrated payment system | Simplified notifications and charges for repairs, enhancing clarity and ease of transactions | Improved customer experience and streamlined financial interactions |
Robust Shipping Tracking | Efficient management of inbound and outbound logistics with strict control and tracking | Ensured accuracy and timeliness in the shipping process, aligning with the client’s requirements |
Repair workflow management | Streamlined inspection process for detailed assessment and documentation of repair needs | High-quality repairs leading to greater customer satisfaction and console reliability |
Digital tracking system | Replaced paper-based tracking with a digital solution, providing real-time repair journey tracking | Enhanced transparency, efficiency, and faster turnaround times in the repair process |
This partnership underscores the profound impact that innovative, customer-centric solutions can have on operational efficiency and consumer loyalty.
Depot repair is more than a mere back-end operation; rather, it emerges as a strategic element that significantly shapes the customer experience and brand reputation.
You can learn more about our depot repair solutions here.